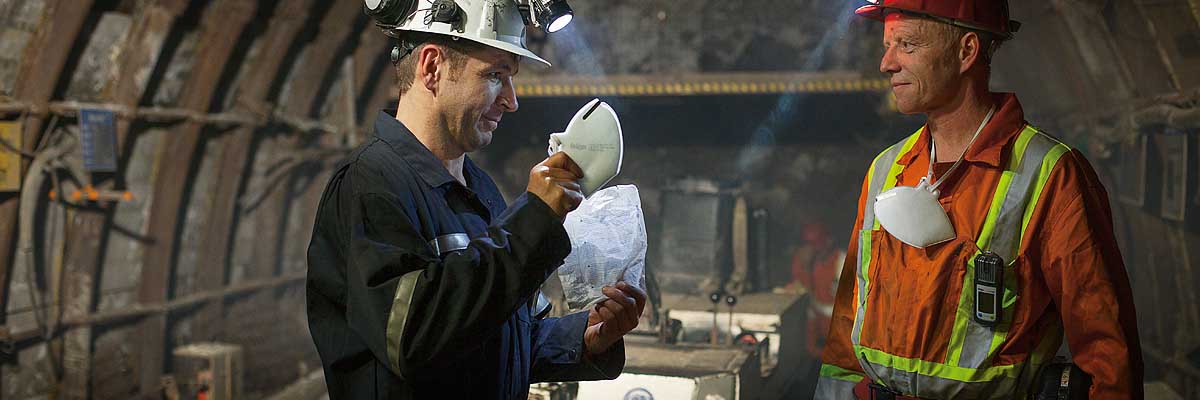
Mining gas detectors: protection against NO2 and HCN
Existing dangers in mines expose workers to hazards that can potentially cause occupational diseases or fatal injuries. When working in confined underground environments, miners may be exposed to hazardous airborne materials released by diesel engines, silica or tailings from the extraction process, increasing their risks of contracting an occupational disease.
One of the primary objectives for companies trying to lower the risks is to create a work environment conducive to employee and contractor facilitation on the prevention strategy. For several mining companies, improving health and safety is a project that is continually evolving towards a “zero injury workplace” objective. Concerning gas detection, choosing the right equipment supplier, as well as maintenance and certification services may be decisive in dangerous situations, both in accident prevention and the response time of the continuous monitoring equipment.
Nitrogen dioxideWorkers from the mining sector are more likely to be exposed to diesel particles, carbon monoxide, aldehydes, nitrogen oxides and other emissions at higher concentrations than what can be found in other workplaces. Diesel engines can be a major source of contaminants in underground environments. Nitrogen dioxide (NO2sub) is a highly toxic gas from diesel engines and blasting emissions. Nitrogen dioxide (NO2sub) is virtually imperceptible to humans.
In the mining industry, diesel engines produce nitrogen monoxide (NO) as a combustion by-product. In the presence of air, NO almost immediately reacts with the oxygen in the air to become NO2sub. Except for specific drilling equipment and specialized applications, most mechanized equipment used in metal mines nowadays is powered by diesel.
Blasting is also causing NO2sub emissions. During an explosion, explosive materials produce a cloud of reactive substances, and the most toxic of them is NO2sub.
Blasters are aware that gases produced by an explosion are harmful to human health, and generally wait for the gases to dissipate before authorizing anyone to return to the explosion site. Yet, people are less concerned about the NO2sub that remains in mining residues. However, gases present in mounds of tailings are mostly fumes from the explosion and they do not dissipate.
Hydrocyanic acidApart from nitrogen oxides, mining workers risk exposure to other chemical compounds such as hydrogen cyanide. Sodium cyanide is very often used in mineral exploitation, and especially gold. Cyanide leaching had been the industry’s gold processing standard for the last 100 years. During cyanide leaching, a cyanide solution, or leachate, is leached by the mineral ore in vats, columns or clusters. Gold is dissolved by cyanide and then retrieved from the clusters or columns. Then, it is extracted from the supersaturated leachate via carbon adsorption or resins. This mineral extraction process is profitable and proven, offering maximal recovery for many gold ores, including low-grade ores and certain refractory ores. The alkaline cyanide solution used in this extraction method is stable and generally safe. However, when the solution’s pH drops below a certain point, the solution can emit hydrocyanic acid, or hydrogen cyanide, a highly toxic gas.
Hydrocyanic acid (HCN) causes death by asphyxiation, preventing breathing at a cellular level (cellular and tissue asphyxia). The severity of the symptoms depends on the exposure time and the chemical agent’s concentration. Among the possible long-term effects are headaches, weakness, change in taste and smell, throat irritation, vomiting, dyspnoea exertional, watery eyes, abdominal colic, excessive salivation, nervous instability and thyroid gland swelling.
In the workplace, exposure to hydrogen cyanide can occur when in contact with vapours or liquid due to its boiling point close to room temperature (25.70°C).
The smell of hydrogen cyanide can be detected from 0.58 ppm. This value is lower than the ceiling value (10 ppm), the IDHL (50 ppm) and the LEL (5.6% or 56,000 ppm). In some cases, it can be a warning sign for a potentially dangerous exposure. However, certain people are completely unable to detect the bitter almond odor, a characteristic of this product, and smell perception is variable according to each individual. It is only when using a measuring instrument that it becomes possible to identify a product and quantify the concentration.
How to protect yourselfEmployers must develop and implement safety measures and methods to analyze the raw exhaust gas from diesel engines used in underground mines and the presence of potentially harmful chemical compounds derived from blasting and other ore extraction activities.
- Analysis of the current levels of contaminants
The first step is to determine the level of contaminants in order to verify if the work environment is safe. It includes environment validation after blasting, verification of the ventilation and exposure evaluation of high-risk work environments. Confined spaces are often risk areas and require continuous gas detection, particularly for operations presenting a risk of exposure to HCN.
- Constant environmental monitoring
After applying corrective measure, it is necessary to constantly monitor the environment – especially in zones where workers are most likely to be exposed to NO2sub, such as miners working with or near diesel engines, in a poorly ventilated area or, near gathering operations of tailings or grinding.
HCN release can be an indicator of an unstable solution. Therefore, control processes via the stationary surveillance of HCN can be used in strategic points. High-risk zones of HCN release can also be monitored to warn the staff before entering a specific area.
Gas detectors: solutions from DrägerDräger – a leading supplier to the mining industry globally - offers one of the most reliable ranges of portable, area and fixed gas detection devices on the market, with a detection capability of more than 500 different gases.
Portable gas detectors used on a daily basis must be as small, lightweight and reliable, but also offer top performance. With a high sensitivity, a wide selection of identified gases, an excellent long-term stability and quick response times, the users of Dräger detectors are certain to be warned quickly and reliably in the presence of hazardous gases.
Dräger X-am® 5600Featuring an ergonomic design and innovative infrared sensor technology, the Dräger X-am 5600 is the smallest gas detection instrument for the measurement of up to 6 gases, including low-concentration NO2sub and HCN.
Small, light and easy to use - the robust and watertight gas detector X-am 5600 is designed for single-handed operation in tough industrial environments. Water- and dustproof according to IP 67 and with an integrated rubber boot, the device provides optimal functionality even under harsh conditions.
In combination with the Dräger X-zone 5500 the gas detector can be used for various area monitoring applications. Up to 25 Dräger X-zone 5500 units can be automatically interconnected to form a wireless fenceline. This interconnection of the area monitoring devices allows for the fast securing of larger areas.
100% compliant: equipment management programSPI Health and Safety’s team of experts is at your service to optimize the purchase or rental of Draeger gas detectors that meet business needs. Our teams ensure the maintenance, inspection and certification of your equipment in our workshops or at your facilities with our Services Are Mobile (SAM). The SPI maintenance mobile teams endeavor to anticipate the safety and compliance needs of companies to prevent mining work stoppage.
The SPI technicians are certified by our manufacturers to their standards.
SPI offers an equipment management program with the objective of optimizing the accident prevention program and to minimize potential production shutdowns.
- Registration of each inspection, calibration or certification according to the manufacturer’s specifications (monthly, quarterly, biennial or annual inspections)
- Automated reminders, including the list of expiring equipment
- Processes and actions required to ensure the compliance and proper functioning of the equipment
- Gas detection equipment rental
- This program prevents purchasing cost investment
- The rental equipment is programmed according to the company’s needs
- Quick quantity adjustment according to your needs
- Rental available during equipment repairs
- Guaranteed compliance
- Financing program available
Purchasing of gas detectors
- Equipment after sales control and follow-ups
- Best cost per use according to your long-term use
Contact our team of experts to implement a management program for your company’s gas detection equipment to optimize your teams’ safety and performance and to review the superior cost of ownership and performance offered by Draeger sensors and gas detection.