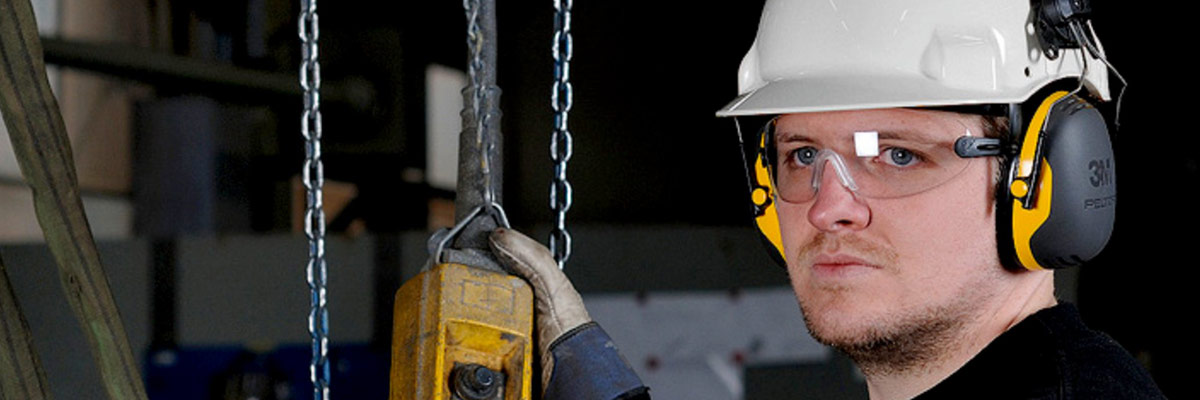
How to develop an effective hearing conservation program (HCP)
Our sense of hearing is vital for communication, experiencing the world, and staying safe in our environments. When hearing loss becomes a common, irreversible issue, organizations must take proactive steps to prevent it.
The Core of a Hearing Conservation Program (HCP)
Hearing loss prevention is at the heart of any HCP. The program involves seven key steps: Measure, Evaluate, Fit, Standardize, Control, Motivate, and Re-evaluate.
Causes of Hearing Loss and Noise-Induced Hearing Loss (NIHL)
According to the World Health Organization (WHO), over 5% of the global population suffers from disabling hearing loss. While some causes are beyond our control (genetics, diseases, aging), excessive noise exposure is entirely preventable.
Noise-Induced Hearing Loss (NIHL) is the most common preventable occupational injury. Key characteristics include:
- Permanent and progressive
- Bilateral (affecting both ears)
- Painless and invisible trauma
- Unnoticeable in early stages
- Cumulative with each over-exposure
NIHL also increases the risk of workplace accidents—workers with hearing issues are twice as likely to suffer injuries. Industries with higher exposure include agriculture, mining, construction, manufacturing, utilities, transportation, and the military.
What Are the Signs of Noise Issues in the Workplace:
- Ringing or humming in the ears after noise exposure.
- Difficulty communicating without shouting.
- Temporary hearing loss after leaving work.
If these signs are present, it’s time to measure environmental noise.
Step 1: Measure
Monitoring noise exposure is the first step. Per OSHA standards, an HCP is required when employee noise exposure equals or exceeds an 8-hour time-weighted average of 85 dB.
Monitoring Methods:
- Area Sampling: Using a sound level meter for instant or continuous readings in specific areas.
- Personal Sampling: Using a noise dosimeter attached near the ear to measure real-time exposure.
While these methods measure unprotected exposure, in-ear exposure monitoring provides the most accurate data by measuring actual noise exposure inside the ear, ensuring real-time monitoring and safety alerts.
Step 2: Evaluate
Evaluation involves reviewing audiograms, hearing protection data, and clinical histories.
Audiograms track hearing sensitivity over time. Baseline audiograms are conducted within six months of initial noise exposure, followed by annual tests.
Hearing Loss Categories:
- Normal: 0-25 dBHL
- Mild: 25-40 dBHL
- Moderate: 40-55 dBHL
- Moderate to Severe: 55-70 dBHL
- Severe: 70-90 dBHL
- Profound: 90 dBHL+
Results must be provided to employees at no cost and retained for the duration of employment.
Step 3: Fit
Fit testing ensures that Hearing Protection Devices (HPDs) provide optimal protection.
Benefits of Fit Testing:
- Meets regulatory training and documentation requirements.
- Educates employees on proper use and the importance of protection.
- Helps select the most effective HPD for individual needs.
Step 4: Standardize
ANSI standards serve as a reference for the calibration of noise measurement equipment and audiometers.
In terms of regulations, the Occupational Health and Safety Regulation (RSST) specifically refers to the following standards:
- CSA Z94.2-2014 – Hearing Protectors: Performance, Selection, Care, and Use, which guides the estimation of hearing protector attenuation.
- CSA Z107.56-13 – Measurement of Noise Exposure, which regulates measurement methodology.
These standards are themselves based on ANSI references.
Additionally, OSHA enforces rules regarding:
- The estimation of hearing protection equipment attenuation.
- The accurate record-keeping of noise exposure and worker protection.
Step 5: Control
When noise levels exceed limits, engineering and administrative controls are the first lines of defense:
- Engineering Controls: Modify equipment, isolate noise sources, or alter the work environment.
- Administrative Controls: Rotate employees to limit exposure or provide quiet areas for breaks.
If these controls aren’t sufficient, appropriate HPDs must be provided.
Choosing the Right Hearing Protection Device:
- Environment: Climate, work type, and additional PPE requirements.
- Noise Reduction Rating (NRR): Lab-tested noise reduction level.
- Personal Attenuation Rating (PAR): Actual measured attenuation from fit testing.
- Comfort: A critical factor for consistent and correct usage.
Step 6: Motivate
Even the best HPDs are ineffective if not used correctly.
Motivation Strategies:
- Educate employees on the risks of NIHL.
- Provide training on proper HPD usage.
- Share annual audiogram results.
- Recognize and reward compliance.
- Offer one-on-one coaching sessions.
Step 7: Re-evaluate
Continuous evaluation ensures program effectiveness. This includes:
- Gathering employee feedback.
- Reviewing noise exposure records.
- Assessing HPD fit and effectiveness.
- Updating training and protocols as needed.
An effective Hearing Conservation Program isn’t just about compliance; it’s about protecting the health, well-being, and productivity of your workforce. By following these seven steps, organizations can create safer, healthier workplaces where hearing is preserved for life.
Learn more about our health and safety trainings →