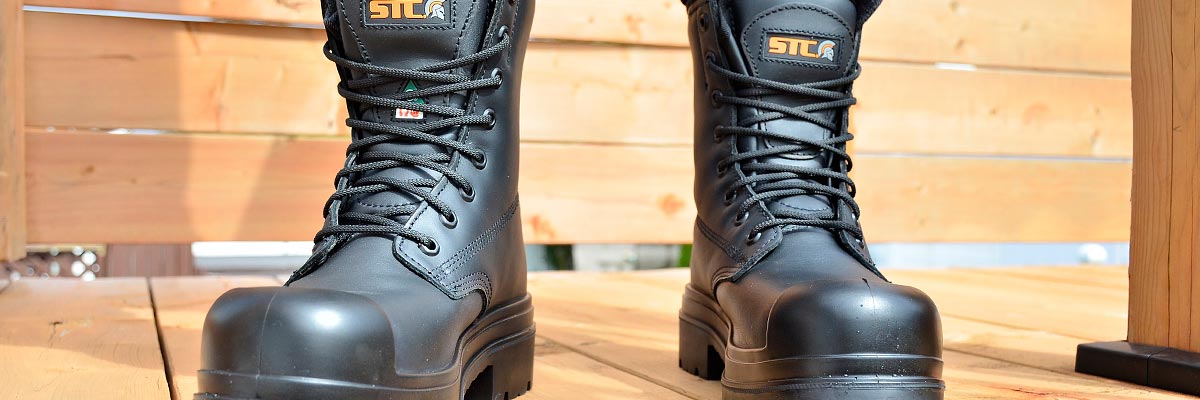
The right safety footwear for you and the right outsole for your work!
When it comes to choosing safety footwear, there are several elements to consider. First, the shoe or boot, and more precisely the outsoles, must be tailored to the reality of the wearer. Selecting the right sole for the right application ensures the wearer efficient protection while reducing the risk of injury and increasing productivity. Other characteristics to consider are the comfort, lightness, thermal insulation and ergonomic design.
For selecting the right outsole, two elements must be examined: the type and condition of the surface.
It is important to distinguish between the two choices offered to the user. The first outsole category is made of rubber with a PU core. It is an average weight outsole that provides excellent abrasion resistance and superior grip on multiple surfaces. This sole remains flexible at all temperatures with a high resistance in extreme temperatures. Another option is the polyurethane outsole. With a weight lower than average, it also offers great abrasion resistance, but the adherence is variable according to the surface (with, among others, excellent adherence over temperate oily surfaces). It only remains flexible in temperate conditions (it hardens in cold weather and deforms in intense heat).
Dry surfaces? Here are the options:
- Is the surface dry? If yes, is it smooth or textured? If smooth, a polyurethane outsole is the logical choice because of its lightness, but the rubber outsole may also be a good option with its better grip. As both outsole types are good, other characteristics, such as comfort, will determine the choice.
- Is the surface textured? If yes, the polyurethane outsole is the logical choice with its high-resistance to abrasion, flexibility and lightness.
Humid and/or oily surfaces? What are the reasons why?
- Is the surface in contact with mineral oils? If yes, the best option is the rubber outsole due to its resistance to that kind of product. Therefore, it is important to choose an outsole with a thread that promotes the evacuation of water and oil when the worker is moving around.
- Is the surface in contact with animal or fish fats? The evident option would be the polyurethane outsole designed for superior adherence and resistance to animal oils. Once more, make sure that the outsole has a thread that promotes the evacuation of oils.
Is the work surface uneven and rough? Our recommendation is the rubber outsole for its durability and grip. The polyurethane outside can also be a sensible choice for its lightness and good abrasion resistance.The surface temperature also has a major impact on the choice of the right outsole. At high temperatures, the Vibram FIRE & ICE outsole is the preferred choice because of its technological development specifically for these temperatures. Even in extreme temperatures, it maintains increased resistance to abrasion as well as excellent adherence.
On a cold and dry surface (for example, concrete, ceramic and steel) between 0⁰ and 10⁰C, both types are interesting: polyurethane for its lightness, rubber for its increased adherence.
On cold and snowy surfaces (from -10⁰C to 0⁰C), rubber outsoles are perfectly suited, but it is important to choose one with a thread designed for good traction when the user is in motion.
On frozen surfaces, in the presence of dry ice or snow, and fairly cold temperatures (-20⁰C to -10⁰C), the Vibram FIRE & ICE rubber and Acton 4GRIP outsoles provide excellent adherence if combined with a thread designed for great traction while the user is in motion.
For temperatures between -5⁰C to 5⁰C, on wet ice, the Vibram Arctic Grip and Acton 4GRIP ICE rubber soles offer the best stability. The abrasive inserts act on the water covering the ice for efficient traction in extreme conditions.