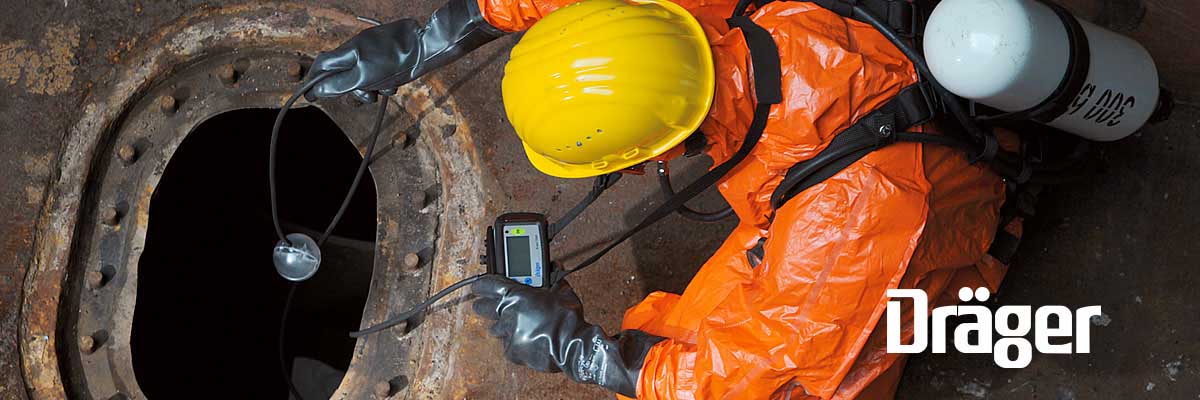
Understanding the most important aspects of a gas detector
How to select the gas detector that will ensure the safety of workers and help your company save time and money? Several models with constantly evolving technologies are available on the market. It is therefore very important to understand the available features and options to make an informed decision.
The five most important aspects of a gas detector
1 - Accuracy
When it comes to gas monitoring, accuracy is open to each manufacturer's interpretation. Officially, accuracy is a statement expressed as a percentage of the closeness of the reading on the gas monitor to the actual concentration; many manufacturers use this as an umbrella term representative of much more, including resolution and sensitivity. To acquire the most comprehensive insight into how the device will perform when used on your work site, it is important to review the following separately.
- Accuracy: Typically listed with a plus or minus 5 percent, it is associated with a confidence interval of 95 percent. This means in 95 out of 100 results; the readings should be within plus or minus 5 percent of the actual gas concentration. It is important to understand the device’s measuring range to determine whether or not the reading could be close to an actual concentration or completely off the mark.
- Resolution: This refers to the reading on the display of the monitor. Typically, sensors should have a resolution finer than the accepted occupational exposure limit for the target gas.
- Sensitivity: Indicates the lowest detectable reading that can be reliably measured and displayed. It is an absolute quantity of the gas that can be detected.
By reviewing each of these individual metrics, you will be in a stronger position to select a gas monitor that will help you optimize on-site safety.
2 - Cross-sensitivities
Manufacturers attempt to design sensors for a specific gas or vapor, however, quite often the target gas is not the only gas detected by the sensor as a result of cross-sensitivity (a sensor's reaction to an interfering gas). Cross-sensitivity can result in either positively or negatively skewed results. For example, positively skewed results can lead to the belief that there is too much of the target gas present, which will result in the implementation of preventative measures such as increasing ventilation or removing the gas hazard. Negative effects produced by cross-sensitivities may cause workers to believe the instrument has malfunctioned or, in a worst-case scenario, cancel out the reading of the target gas, thus potentially creating an even more dangerous situation that can be life threatening.
Ultimately, the best way to prevent interference from outlying gases is to be aware of all agents associated with each test site and their effects on readings when detected. This will aid in purchasing a gas detector suitable for your intended use and environment, as well as in identifying which additional filters are necessary to prevent falsely enhanced readings.
3 - Reliability
One of the selection criteria for a performing gas detector is its durability. Ambient conditions in a workplace, in particular temperature, pressure, and relative humidity, can impact the detector durability and reliability. We must rely on the manufacturer’s information to determine what different factors may influence the readings.
To assess the reliability, you also should consider its test repeatability. By revealing how often a device achieves the same results under the same ambient conditions, it demonstrates how the monitor can be expected to act during identical conditions, test after test.
For more details, you can refer to Drager Sensor and gas detector manual.
4 - Response time
In the oil and gas industry, the sensors’ response speed allows the workers to be alerted of unseen hazards as quickly as possible. Fast response time (t90) refers to the time it takes for the monitor to display 90 percent of the actual concentration. This is a critical consideration in selecting a gas monitor that will help you make safety a work site priority.
For example, a gas detector device with a t90 time of 25-40 seconds could expose a worker to hazardous levels of gas for almost 45 seconds more than a detector with a t90 time of 15 seconds. This exposure difference could be enough to cause eye and throat irritations, headaches, dizziness, nausea, coughing and breathing difficulties depending on the type of gas present.
By selecting devices with fast response times for your gas detection toolkit, you contribute to the prevention of fatalities and a stronger safety culture.
5 - User-friendly devices keep safety simple
Simple, effective equipment will always result in greater compliance and more frequent use, therefore enhanced safety. That's why it is of the utmost importance to choose the gas monitor that seamlessly integrates into workers' everyday routines. Characteristics to look for in a gas monitor include:
- Lightweight and unobtrusive solutions equipped with proper attachment features so they are comfortable for the user to wear in the breathing zone on the chest pocket, collar, or hard hat.
- Durable, shock-proof devices with a chemical-resistant coating that will withstand the rigors of the work site.
- Cost of parts: Universal-part gas detectors.
- A monitor capable of recording large amounts of data, as well as transmitting the data wirelessly to a central command station for analysis.
- Automatic bump and calibration tests as soon as the lid of the device is closed to foster daily use.
- Flexible and portable devices that don't require electricity.
Gas detector manufacturers are in constant competition to create and develop equipment that can do it all while still protecting workers. To navigate your next purchase effectively, it is essential to develop a stronger understanding of these important features that foster greater security. After all, by getting to know your gas monitor, you lead the way to a safer working environment for you and your colleagues.