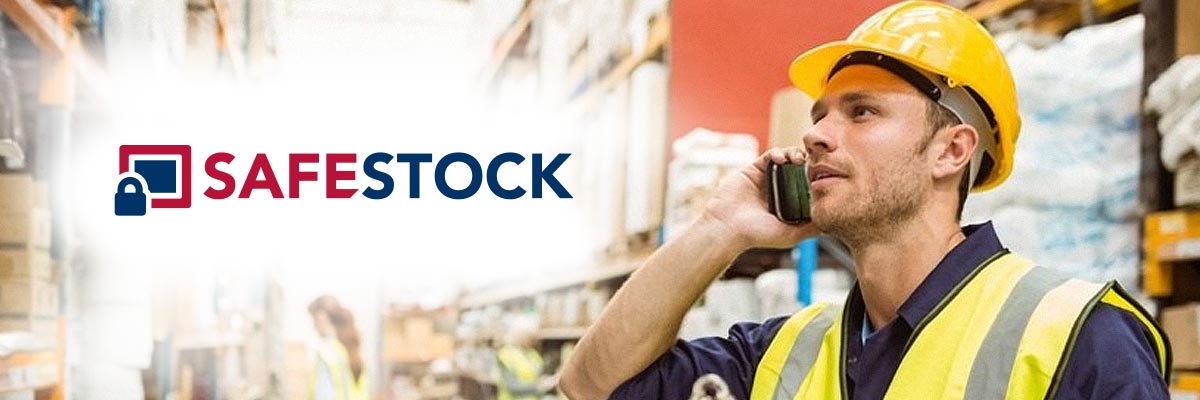
4 Tips on Implementing a Vendor Managed Inventory
Have you ever wondered if there was an easier way or a more efficient approach to managing your inventory?
Perhaps this question has crossed your mind in the past... Either when you were reordering an item you had purchased or when you realized that you had too much inventory sitting around in your warehouse for a while.
And unfortunately, it all adds up quickly: time, money, resources, and space can all too often be wasted because of imperfect inventory management.
Re-evaluating your inventory management system can help you achieve corporate goals such as automating your operations, improving productivity, and ensuring the safety of your employees. Let's find out what our experts have to say!
What is a Vendor Managed Inventory system?
Vendor-Managed Inventory is an approach that entrusts the management of your inventory and procurement to a trusted partner.
Typically, the partner installs the right management system for your needs by sending a representative or expert to your site. The management system can vary and may include barcoded labels, vending machines, boxes, and much more.
This system then allows your partner to track the amount of inventory used, replenish it without worry, provide reports, and automate many internal processes.
What is SafeStock?
SafeStock is our occupational health and safety (OHS) inventory management service that provides a range of systems and technologies for the automation of your inventory and supply chain management processes. This level of automation results in significant time and cost savings.
For workplace safety, here’s how SafeStock can help:
- Your team ALWAYS has access to the right personal protective equipment (PPE)
- Restriction applications to ensure your employees use the proper PPE for their tasks (e.g., restricting a specific glove model to a team because it doesn’t offer the correct type of protection for them).
Our experts will find solutions tailored to your needs. Protect your workers by ensuring the right PPE is available at all times!
Our tips for simple, effective implementation of an inventory management system
-
Talk to an expert
The first step is simple: talk to one of our experts! They’ll be happy to tell you more about our program. Most importantly, they’ll be able to guide you to a solution that’s right for you. We offer a wide variety of tools and technologies to our customers to make sure that there’s always a solution to suit everyone’s needs.
-
Involve your team
We encourage you to get your employees involved. Why? Because, at the end of the day, they’re the ones who’ll be working with the system on a daily basis. So they may have some excellent recommendations about which products to include, how to configure and how to manage the areas. Involving workers also means offering them the opportunity to have a say in those decisions that will have an impact on their working environment.
Make sure they have all the tools and that they understand the impact of the management program. Fortunately, our system will make their lives a whole lot easier!
-
Share information with the supplier
For effective inventory management, it’s best to build solid communication with your supplier. This will allow you to manage your expectations so that the inventory management process will be a success. You’ll also need to communicate all the necessary information concerning inventory data. That way, you will confirm the right process to be put in place.
-
Take this opportunity to review your product list
This pivot to vendor-managed inventory is the perfect time to review and update your product lists. All too often, we don’t take the time to upgrade the equipment we need to use. Take the opportunity to review this list and include only equipment that will actually be used, thus limiting losses and large sums of money. It will also optimize your employees’ protection by selecting the right equipment for their reality.
Need help with this step? Luckily, we’re specialists in workplace safety!
Implementing SafeStock is a win-win situation
Implementing an inventory management program is not trivial! Complete or partial automation of your systems cannot be done at once.
Depending on your situation, our experts will offer you the best recommendations for your system.
You can focus on one or more critical aspects, and then add other parts to your management program. By familiarizing yourself with the process on a smaller scale, adding and automating your systems will be much less overwhelming.
This allows you to identify unforeseen issues more easily and realign your focus for the next steps.
Partnering with SPI as your health and safety provider pays off and is safe!
Contact our experts today.
Together, we’ll find and create a solution customized to your business so that you can focus on the important things.