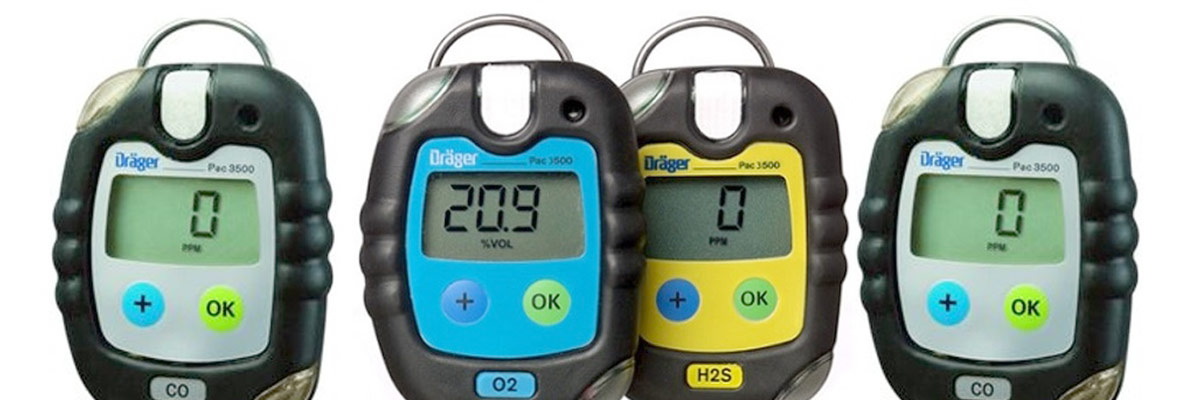
A guide on the four types of gas detection sensors
There are many areas where flammable and toxic gases and vapors occur, and they pose a great danger to all – and that is the purpose of gas detection and warning devices – to better protect employees.
Flammable and toxic gases and vapors measurements can be done in three different ways: by temperature, pressure or volume. All gases are potentially dangerous in their liquid, compressed, or normal state – the decisive factor is their concentration.
Knowing that each device and each measurement principle have its strengths and limitations, selecting the right measuring device is essential for gas detection. And a fundamental element in choosing the right device is to have a general idea of the gases and vapors present in the work environment.
The choice of the right tool depends on critical factors:
- The risk of explosion
- The lack or excess of oxygen
- The toxicity
- The cross sensitivity
Draeger manufactures four different types of sensors.
An electrochemical or EC sensor measures the concentration of a target gas by oxidizing or reducing the target gas and the electrode is measuring the resulting electrical current output. These types of sensors are used for detecting oxygen and toxic gases.
A catalytic, Cat EX or combustible sensor oxidizes a combustible gas and converts the temperatures change into an electrical signal. These types of sensors are used for detecting combustible gases, such as methane, propane and hydrogen.
An infrared or IR sensor measures trace gases by determining the absorption of an emitted infrared light source through an air sample. These types of sensors are used for detecting carbon dioxide and a wide range of combustible gases.
A photo-ionization detector or PID breaks molecules into positive and negative charged ions and measures the electrical charge of these ions using a detector to display the amount of gas or vapor that is present. These types of sensors are used for detecting volatile organic vapors (VOCs) and toxic gases.
Electrochemical Sensors
The basic principle behind an electrochemical sensor involves at least two electrodes, which interact with each other in two ways: first, through a liquid electrolyte and, second, through an external electrical circuit.
First, the gas needs to pass through the membrane to enter the sensor chamber. This membrane is made of a hydrophobic material that is designed to keep water from getting into the sensor and keep the liquid electrolyte from getting out of the sensor. The gas enters the sensor chamber and a chemical reaction takes place in what is known to be the three-phase zone, where gas, the electrodes and the liquid electrolyte meet. This chemical reaction generates an electrical current which is measured by the external electrical circuit.
A dual-electrode sensor does, however, have many drawbacks. For instance, if high concentrations of gas occur, this leads to higher currents in the sensor. This high current leads to a lower voltage inside the sensor, and can cause unusable readings or, in the worst case, can cause the chemical reaction inside the sensor to stop during the measurement process.
That’s why the Dräger XS and XXS sensors contain a third electrode known as the “reference electrode”, which does not have a current passing through it. It continuously measures the sensor’s voltage at the measuring electrode, which can be corrected using the sensor’s control circuitry. This produces a considerably improved measuring quality and a longer lifetime.
Once exposed to fresh air, the chemical reaction to the gas is reversed on the counter electrode, taking the sensor back to its original state.
Catalytic Sensors
The catalytic sensor is the most common type of sensor for combustible gas measurement.
The gas to be measured enters the sensor chamber through the flame arrestor. The flame arrestor prevents the energy from the oxidation process taking place inside the sensor from getting back out into the atmosphere. The element’s heated catalyst, which is about 500 degrees Celsius, facilitates the reaction between the gas entering the sensor and the oxygen in the air.
This reaction causes the element to heat up to even higher temperatures. The increase in heat causes the electrical resistance of the element to change. This change of resistance is what is measured to provide the reading on the display of the gas monitor.
Just like with the electrochemical sensor, one of the sensor elements, in this case, a heated catalyst, is used only to compensate for changes in environmental conditions.
The higher the level of gas entering the sensor chamber, the higher the temperature of the measurement element, which means a higher reading on the display.
For proper operation, a catalytic sensor needs oxygen. If the oxygen level drops too low, the gas will not go through the reaction process effectively and this will give lower than actual readings on the display of the monitor. With Draeger monitors, if the O2 concentration drops below about 8% by volume, the reading of the combustible sensor will be blanked out. Once the O2 levels come back above 8%, the combustible reading will again be displayed. This is used as a safety feature to notify the user of any potential issues with monitoring for dangerous levels of combustible gases.
Infrared Sensors
The infrared sensor is an alternative for combustible gas measurements when there is no oxygen present or for measuring high concentrations of carbon dioxide.
Infrared sensors work on the principle of light absorption. Every gas absorbs light in a particular way, which is why some gases appear as different colors. Some combustible gases, such as methane and propane are called hydrocarbons, and they absorb different wavelengths of light compared to the main components of air (oxygen, nitrogen and argon). This distinction can be exploited to measure the amount of hydrocarbons present.
The gas to be measured enters the sensor chamber through a flame arrestor. The flame arrestor prevents any energy from within the sensor from getting back out into the atmosphere.
The infrared transmitter produces broadband radiation that passes through a window into the sensor chamber, where it is reflected off the mirrored walls, and passes through another window, falling onto the double detector.
This double detector consists of a measurement and a reference detector. The reference detector is not exposed to gas, and is used to compensate for environmental changes. If the gas mixture contains a percentage of hydrocarbons, then some of the radiation is absorbed and the measurement detector produces a reduced electrical signal.
This reduced electrical signal is how the sensor knows when and how much gas is present.
Photo-Ionization Detector Sensors
The Phot- Ionization Detector (PID) is a specialized sensor that is known as a broad-range sensor, as it is not specific to any one gas. A PID will measure a variety of toxic gases and a range of VOCs (volatile organic compounds) in very low concentrations from parts per billion (ppb) up to over several thousand parts per million (ppm), depending on the gas being measured.
The sensor consists of a housing, two electrodes and an ultraviolet lamp. The ultraviolet lamp rating determines which gases will be measured by the sensor.
The gas to be measured enters the PID sensor chamber through the sensor membrane. The photons from an ultraviolet lamp (UV) inside the sensor break down the gas molecules into positively and negatively charged ions. These charged ions are counted by the collector electrode within the sensor and produce an output current that is measured by the instrument’s electronics.
The UV light produces the energy that is required to ionize certain gases. This energy is measured in electron volts (eV), and gases will have a corresponding ionization potential. This is the amount of energy required to break it down into positively and negatively charged ions. Then, these ions can be measured as an electrical current. The strength of this current is directly proportional to the concentration of ionized molecules inside the chamber, making it possible to determine the concentration of the gas in the air.
This sensor becomes important for concentrations of combustible gases that are also toxic at very low levels, where the toxic hazard is reached much faster than the explosive hazard.