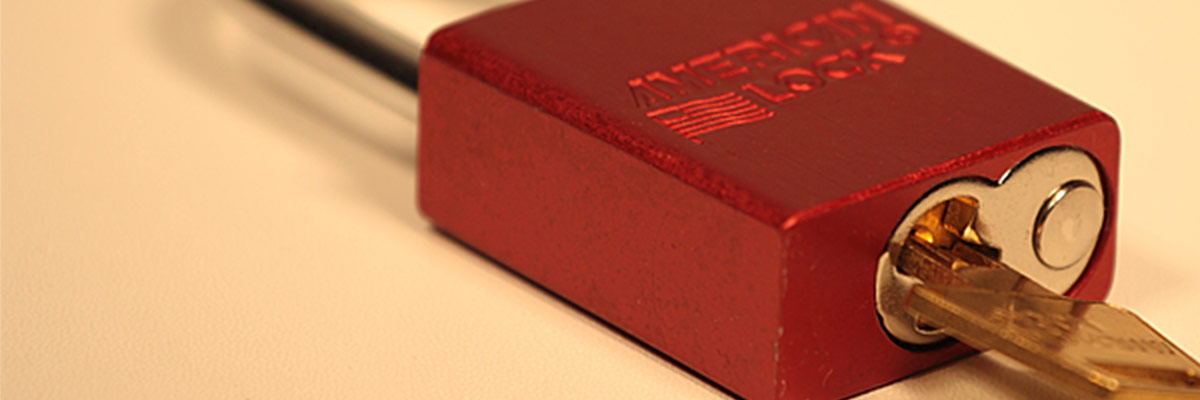
Man versus Machine: lockout/tagout program for machinery
Small and large companies in the manufacturing industry invest tremendous efforts and money in modernizing their automated machinery. However, even if automation reduces the number of human interventions, it does not totally eliminate them, and workers are still facing hazardous situations. Do you have a lockout/tagout program and are all your lockout tags compliant and updated for all your equipment?
The Canadian standard for lockout clearly indicates that the primary method of hazardous energy control is lockout. Machinery technical safety is seen as one of the alternate measures.
When it comes to investing in safety around machinery, we must first understand where the risks of accidents are coming from. Many accidents occur during tasks such as tuning, maintenance, repair or start-up rather than during the operation itself. The absence of guards, lack of knowledge about the equipment and energy sources, lack of safety training for workers, misuse of equipment and protection devices are all elements contributing to increased risks. Still, it should be noted that the main causes of accidents related to machinery automation are missing, incomplete, unknown or not implemented lockout procedures.
Lockout standard in Canada
Did you know there is a significant difference between lockout and machinery technical safety? The Canadian standard for lockout clearly indicates that the primary method of hazardous energy control is lockout. Machinery technical safety is seen as one of the alternate measures.
How do I know if my lockout program is compliant? Do I need to have it audited? Is a compliant lockout tag mandatory for all my equipment? These are all relevant questions but today, we will only discuss the compliance of lockout tag. In 2005, with the implementation of the standard CSA Z460-05 in Canada, the lockout tag has gradually become a requirement and is now mandatory under that standard.
It offers many advantages, including:
- Accident prevention through a rigorous risk analysis
- Harmonization of work practices within the company
- Acceleration of work based on the substantive effort conducted to produce a clear and safe work procedure
- Easier training and education of the staff
- Improved knowledge of risks and operation of equipment
- Appropriate tracking of the system allows the employer to demonstrate due diligence
Lockout tag in 5 steps
- First: Inventory all machinery, equipment and systems, including mobile units on which work and interventions in risk areas are likely to be performed.
- Second: Determine the content and format of the lockout tag used by the company. Warning! The CSA standard requires that the lockout tag meets specific criteria as to its content.
- Third: Implement a pilot project first on one machine in order to test the proposed system. At this step, it is crucial to involve experienced employees and management personnel.
- Fourth: Prepare each tag based on a rigorous risk assessment involving qualified people.
- Fifth: Validate the preliminary tags by qualified personnel who know the functionalities of the equipment well. This validation must include a test ensuring that all proposed lockout methods are efficient.
For more information concerning our lockout and factory health and safety services, visit our website or contact the SPI Health and Safety Consulting Services Team.