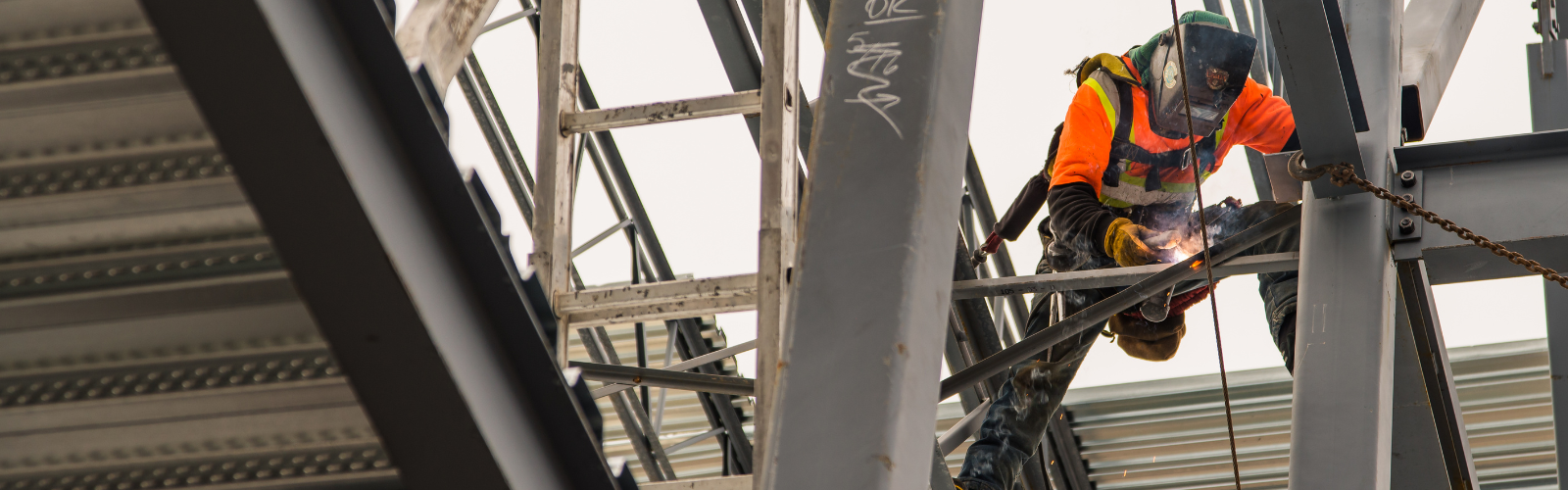
Efficient Fall Protection Equipment Management: 3 Solutions for Your Company
Selecting and using safety harnesses represents an essential element of the health and safety strategy for working at heights. However, the purchasing and maintenance as well as the certification of the equipment can be complex and costly.
Let's take a look at 3 processes that optimize the management of your fall protection equipment.
1. Identification system for fall arrest equipment
As part of a loss prevention program, a company may implement an identification system for fall arrest equipment. Each harness and lifeline can be labelled with a unique number. This type of system minimizes the potential of equipment being stolen while optimizing replacement costs. According to the manufacturer’s instructions, a worker using a safety harness must perform equipment checks before each use. The inspection includes the visual verification of each part to identify all weaknesses, cracks or damage to the harnesses, anchorage straps, lifelines, ropes, rings and carabiners that are part of the worker’s fall arrest protection. Any sign of degradation on fabrics and metallic parts, such as broken seams, signs of mould or any other, must be reported to the supervisor and the equipment removed from service until a qualified person confirms it is in good working order.
Our experts in technical services can support you in the maintenance and inspection of your fall protection equipment!
Equipment identification allows you to retrieve all records for a specific item and, in certain circumstances, to repair it for a fraction of the cost of brand new equipment. It is a tremendous added value. In some situations, the company can replace the worn or damaged parts rather than changing the entire equipment.
2. Inspection and certification traceability
In addition to the daily visual inspections, the manufacturer requires a yearly inspection and certification by a qualified person or a specialist to guarantee the compliance of the fall protection equipment.
Companies that adopt a proactive maintenance strategy can see a reduction in maintenance costs of 25% and an improvement in equipment availability of about 20%!
Equipment certification ensures compliance with CSA standards and regulations as well as manufacturers’ instruction manuals. The serial number assigned by the identification system helps to keep track of the inspection and certification of each piece of equipment while optimizing the performance of the harness and the safety of the worker who uses it. This traceability helps the team to locate the equipment according to the user name, department, project site, etc.
Field iD: Efficient Equipment Management
Is traceability and accurate recording of your inspections and maintenance important to you? Our Field iD platform automatically records your equipment inspections in the database for efficient follow-up.
3. Equipment standardization
The implementation of a system for the standardization of equipment facilitates the selection of material that meets the principal needs of the company. The equipment standardization across all business divisions allows significant economies of scale while ensuring the highest safety levels for workers.
Learn about the solutions and the actions you can put in place in your company to optimize your costs, and more importantly, to ensure the compliance and proper functioning of your equipment.